March/April Update: Back On Campus!
Announcements
The QLS InvenTeams’ progress update at the Mid-Grant Technical Review in March was an incredible success! With over 80 attendees at the peak, amazing feedback, and a successful presentation, the team members are all immensely grateful to all who joined. It truly was a pleasure to share the project with everyone. Thank you! The event recording is available on Youtube here.
The next and final showcase will be at the EurekaFest on June 15-17!
(Instagram Post - https://www.instagram.com/p/CL-ILZ0Musc/)
Back on Campus! (Partially)
As of late March, the school has finally permitted some level of in-person meetings. Though these only consist of around half the team, stepping back onto campus for the first time in over a year (which is as long as the project has been going) was an immensely gratifying and sensational experience. The team will continue adapting to the pandemic situation as best as possible, and hopefully this return will allow more efficient collaboration. Additionally, plans to the design with Deaf Camp Pacific are intended for the end of April.
(Instagram Post - https://www.instagram.com/p/CN-hHgusv6-/)
Haptic Device Update
With regards to the haptic device, the plan is to encase the electronic systems within a compact 3D-printed housing. This system will ensure durability, waterproof qualities, and removability of the electronics wherein the fabric ankle-band can be washed.
Layout - So far, the team has 3D-printed multiple iterations with different electronic layouts. The goal is to determine if the electronics are more comfortable stacked (taller and more compact) or laid flat (thinner but less compact). After having multiple people wear and compare these modules, it was discovered that the both layouts were relatively comfortable. The stacked layout is still more practical for being significantly more compact and thicker by only 1/8 of an inch.
Vibration Motor - The vibration motor may be mounted to the housing, therefore having a wider surface area but weaker vibration, or placed on its own, with a stronger vibration in a concentrated area. Prototype housing has been modified to accommodate for both setups. Team members experimented by wearing both layouts and concluded that having the motor placed separate from the housing is much easier to feel, as well as more comfortable.
Next Steps - Next steps involve contouring the housing to match a player’s ankle, hence improving the ergonomics. A watertight lid will also improve durability and keep out sweat, and securing the electronics to a PCB breadboard will further boost the rugged design as well as speed up the construction process.
Ergonomic Design #1 - Curved Housing
Ergonomic Design #2 - Separated Housing
PCB Board Concept
Prototype Iterations
CAD Designs
Electronics Housing + Ankleband
Connectivity Issue (Addition of Antenna)
After encountering problems with the connection between the trigger and haptic device, apparently due to the trigger device’s casing blocking the wireless signal, the team plans the addition of an antenna to ensure stable connection. This antenna will protrude from the casing, and the team is experimenting with ways to make it as unobtrusive as possible by avoiding the bulky NRF24 antenna module. Testing is in progress, in conjunction with the development of newer 3D-printed casings.
Trigger Device Update
To avoid tampering with or reprogramming the referee’s whistle, the trigger device will be a completely self-contained module that attaches to the exterior of an electronic whistle. The device’s and whistle’s buttons will align such that pressing it will trigger both a haptic signal and the whistle’s sound. Since the Fox 40 brand of electronic whistles are most commonly used in official games, the team will model the device to contour with the Fox 40 whistle. Future versions will feature an adjustable design that accommodates for a wider range of whistles.
Version 1 of the trigger device is meant as a proof-of-concept, and consists of a rectangular module sitting on the top of the whistle.
Version 2 of the trigger device takes ergonomics into higher consideration, and attempts to contour the shape of the whistle. It also accommodates for the hand placement when the whistle is being held. The overall size and electronics will be compacted in later versions.
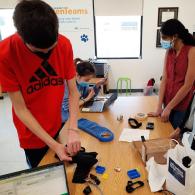